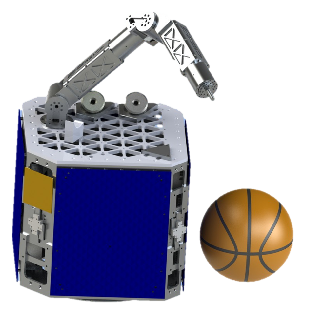
University NanoSat Program (NS-7): Dynamic Manipulation Flight Experiment
DYMAFLEX was sponsored by the AFRL as part of the University Nanosat Program (UNP). UNP is a university competition where students build satellites and compete for a launch. The winner of the compeition is awarded funding to finish the project, testing and help from the AFRL, and a launch. The competition is quite fierce and has been described as 'satellite hunger-games'.
The goal of DYMAFLEX is to investigate the coupled dynamics and associated control mitigation strategies for a free-flying vehicle with a high-performance manipulator performing tasks analogous to satellite servicing. This requires a satellite with a high performance manipulator and a propulsion system.
The DYMAFLEX manipulator is sized to fit onto a microsatellite (~50kg) and therefore will be significant percent of the mass. Consequently, as the manipulator moves, the vehicle base will experience significant coupled dynamics. The control algorithm for the manipulator will need to account for the base motion while the manipulator is in moving. In the past, these coupled dynamics have been reduced to negligible by restricting the speed of the manipulator and mounting them on very large bodies.
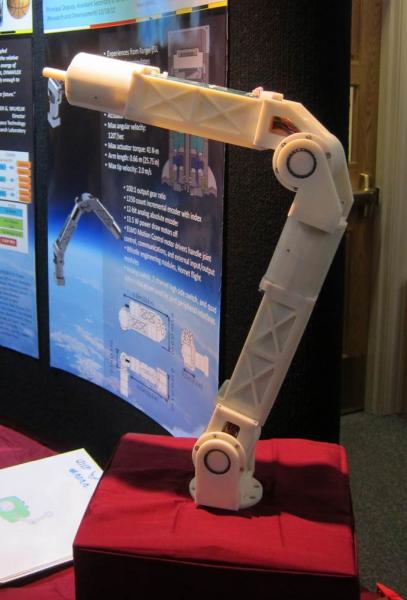
Mission Overview
Investigate the coupled dynamics and associated control mitigation strategies for a free-flying vehicle with a high-performance manipulator performing tasks analogous to satellite servicing
Develop a microsatellite in the university environment through a program which maximizes opportunities for students to be involved in all aspects of the development process
Leverage three decades of advanced space robotics research in the development and flight demonstration of a space manipulator system
Manipulator
The technology behind DYMAFLEX is based on Ranger, a flight qualified shuttle program. Ranger was designed to perform satellite serving. Ranger consists of two manipulators, which have the same maneuverability as human arms. While Ranger was not able to fly due to launch schedules, it was tested extensively in neutral buoyancy. Ranger was used to demonstrate that robotic systems are capable of performing satellite servicing.
DYMAFLEX's manipulator is a lot smaller and lighter than Ranger with an arm length of 25.75 inches. A prototype manipulator was built using a rapid-prototype (3D printer). This prototype is fully function and is capable of the same movement as a metal version.
Manipulator Summary
- 4 DOF
- Actuator Diameter: 6.4 cm
- Actuator Length: 10.4 cm
- Actuator mass: 0.75 kg
- Max angular velocity: 120°/sec
- Max actuator torque: 41 N-m
- Arm length: 0.66 m (25.75 in)
- Max tip velocity: 2.0 m/s
- 100:1 output gear ratio
- 1250 count incremental encoder with index
- 12-bit analog absolute encoder
- 13.5 W power draw motors off
- ELMO Motion Control motor drivers handle joint control, communications, and external input/output Whistle engineering modules, Hornet flight modules
- Analog switch, 2 channel high side switch, and quad differential driver used for joint peripheral interfaces
Acknowledgements
The Dynamic Manipulation Flight Experiment is under development at the University of Maryland Space Systems Laboratory, part of the Aerospace Engineering Department and the A. James Clark School of Engineering.